Dutch
Barn Preservation Society
Dedicated
to the Study and Preservation
of New World Dutch Barns
NEWSLETTER
SPRING 2002, Vol. 15, Issue 1, part two
Logistics
Shocking
This is a job I can remember doing as a young man, about 1933.
On a blistering July day, the three-horse team pulled hard on the
reaper binder. The machine spit out oat sheaves very fast. My cousin
and I would stand these sheaves upright against one and other in
groups of four or six to make a shock. I'm sure the youngsters
of colonial times did the same kind of work as their mother, the
binder, wrapped the sheaves of wheat in 1680.
Hauling
After about a week of drying in the shock the sheaves were
ready to be put into the barn. The bundles would be forked on to
a wagon (4 wheels and two horses) or a cart (2 wheels and one horse)
for transport. They would be neatly stacked to facilitate a large
load and ease of unloading. One man could drive and load while
two men forked. The wagon was driven into the barn on to the threshing
floor and the load was pitched into the side aisle. One or two
men would stack the sheaves neatly on the poles that lay between
the column sill and the sidewall sill. Most of the side aisles
could be filled from wagon height. The loft would require extra
help to move the sheaves to the great height. Once the crop was
all in the barn, urgency disappeared. Phase one of the harvest
was complete.
Threshing
Phase two could take place at a leisurely pace consistent
with other jobs around the farm such as tillage for next years
crop, clearing woodland and growing other food and fiber. The flail
was an age-old tool. A fresco in the Palazzo Publico in Siena,
Italy by Ambrogio Lorenzetti, "Good Government in the Country" ca.1339
shows two characters outside the barn flailing in unison, likely,
to the rhythm of some chantey, as they beat the straw. The Dutch
barn in 1680 provided ample space for this job in complete shelter.
The central portion of floor level, usually 30x50 feet was designated
as the threshing floor. Thick, wide floorboards, usually splined,
gave a hard, impenetrable, surface to work on. A batch of sheaves
were tossed down, from storage, and spread through the center of
the threshing floor. A good number of flailers could work there
together. The staff was grasped with two hands and the beater rod
or swingle (sometimes called a souple) was brought down sharply
against the open sheaves on the floor. This blow separated the
grain from the straw. Yield was reported as seven bushels per man
day. The denuded straw was forked into the side aisle for future
use as livestock feed, bedding, and other uses. The chaff and grain
would be swept to the side for future winnowing.
Winnowing
In this process, the huge barn doors played an important role.
They could be manipulated to control the prevailing winds through
the threshing floor. Open fully or partially, they could act as
a valve to control the volume of air from the north wind, (Barns
usually had north-south orientation.)
With the gable end doors adjusted and all other doors closed,
there would be a steady flow of air to facilitate the separation
of the collection of material left after threshing. As much material
as could be lifted easily would be put in a winnowing basket or
tray. The container was about 4 feet across and had shallow sides
part way around to contain the material. With outstretched arms
the winnower would grasp the tray and toss the contents up into
the moving air with the intention of catching it again as it fell.
As the material was airborne, the breeze would blow away the lighter
material. This would be repeated until all chaff and dirt drifted
away leaving the heavy kernels of grain in the basket. The grain,
ready for the mill, was then bagged. The cloth for bags was probably
made from hemp, a very staple strong thread. Sacked grain was particularly
subject to damage from rodents. Storage anywhere, for any length
of time was risky, The best defense was the regular shipment to
the mill where the grain would be sold or the flour returned for
domestic use and kept in barrels.
Another method of winnowing was by the use of a shovel or scoop.
With this tool, a pile of material on the floor was attacked with
the shovel. A shovel full was thrown into and against the wind.
The heavy material traveled the furthest and the lighter, "tailed'" away
along the floor. At the head of the resulting pile was the grain
for the mill. The less desirable part for home use and livestock
feed. This very scene was caught on TV recently, being carried
out in modern China in the production of rice.
The culture of wheat in the late 17th century included practices
that had existed for hundreds of years. The only new thing was
the huge barn with the processing area inside.
Using 157 farms in Kings County as specific examples, (DBPS Newsletter,
spring 2001 page 7) there emerges a picture of a typical farm of
50 acres, occupied by seven people. The taskmaster, faced with
a deadline of four 1/2 weeks in which to harvest 32.3 acres of
wheat, might make the following assignments:
Reapers 1 .5
Binders 1.0
Shockers .5
Teamster 1.0
Loaders 2.0
Total Field hands 6.0
The pace of the work would be set by the 1.5 reapers, each covering
.66 acres a day. This would take 50 man-days or 33 calendar days,
well within the time limits. Work in the barn, threshing and winnowing
would take another 65 man days before all the bagged grain was
ready for shipment.
The barn was especially adapted to compartmentation. The space
could be segmented between the bents in the side aisles, and designated
for different crops. The space could have been shared with neighboring
farms as well. The barns capacity could easily have accommodated
five farms like that above. (DBPS Newsletter Spring 2000, page
5)
Most of each farm was devoted to growing grain, and the late
summer landscape was a beautiful quilt of golden yellow. Almost
all of the community, which was 95% rural, got involved in the
harvest. This would have been necessary in order to meet the requirements
that had developed for food and exports.
In the next issue, we will discuss the engineering, STATICS, of
the barn.
LEST WE FORGET
Recently I was asked, "Why preserve the American Dutch Barn?"
When you truly believe in something you don't have to keep convincing
yourself of the fact. I was not ready for the question and it took
me by surprise. I had difficulty answering. The usual cliches, "History,
Heritage, and joinery" did not express my deep feelings for
the subject. These can be relegated to a history book.
Later I found the real reason to save the barn, "It is a
work of art." For me, this is not an unusual observation for
I am a serious amateur artist. I have frequented museums and galleries
for most of my life and I always come away from these places stimulated
and impressed. That is how I feel standing on the threshing floor
of a well preserved American Dutch barn. The Wempl the Wemple,
and even the replica Graulich barn are great examples. They
can stir one's soul and this feeling cannot be relegated to a book.
Many years ago the Metropolitan Museum of Art paid the record
sum of two million three hundred thousand dollars for the Dutch
master painter Rembrandt's ARISTOTLE CONTEMPLATING THE BUST
Of HOMER. I saw it. There was no question of preserving
that painting. Rembrandt died in 1669, not long before the first
American Dutch barn, VAN BERGEN in 1680. We carry
on the Dutch artistic tradition, with the authentic, preserved,
barn buildings of today. The editor.
Drawing: FANCY SCARF, taken from column sill at
the Lazzari Barn in Rotterdam, New York.
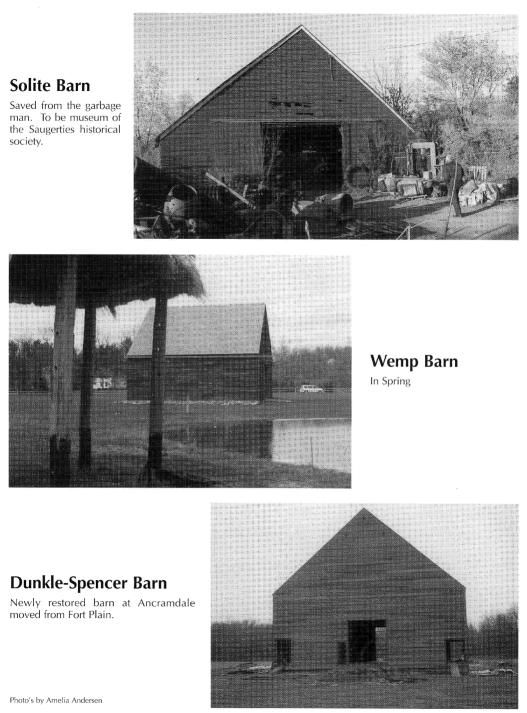
|